- Details
- Written by: Phil Threlfall-Holmes
- Category: Uncategorised
- Hits: 839
- TH Collaborative Innovation: TH Collaborative Innovation
Prof Phil Threlfall-Holmes
Founder of TH Collaborative Innovation.
Visiting Professor in Mechanical Engineering at The University of Leeds
My work links formulation, product microstructure, rheology and spray performance. Before starting THCi in 2014, I spent 18years with ICI and AkzoNobel developing products and processes, including spray drying, spray freezing and freeze drying, spray painting, and atomiser and lab characterisation instrument development. Although my current role is largely experimental spray characterisation, rheology, data analysis and interpretation; instrument mechanical and elecrtrical hardware design and software development and integration, I originally graduated in Chemical Engineering from Christ's College, The University of Cambridge. My PhD in Spray dryer Modelling was done part-time, whilst having the full time day job at ICI.
Why Collaborative Innovation? Because no one person knows all the answers. I can assist you in your product development by working with you and your team to broaden and deepen the expertise of your own team. I can also connect you with my network of independent professionals and academics with complementary knowledge.
Tobias Threlfall-Holmes
Engineering student at Durham University.
Tobias' wrote validation software for the ROJER-X timing controller, and did experimental testing and troubleshooting of both the ROJER-X and THCi-developed ImageJ plugins for spray characterisation whilst at The University of Liverpool Maths School.
- Details
- Written by: Phil Threlfall-Holmes
- Category: Uncategorised
- Hits: 832
- TH Collaborative Innovation: TH Collaborative Innovation
This matters to spraying paint, hairspray, surface cleaners, agrochemical crop spraying, spray-dried products like coffee and pharmaceuticals... etc. A very non-exhaustive list, there are hundreds of applications.
Get it right, and we can reduce overspray (in some cases with real commercial formulations, by up to a factor of 10).
Get it wrong, and we ruin the spray.
Sadly, it's easy to get it wrong, and really hard to get right: it takes knowledge, skill, experience, and novel instrumentation.
-------------------------------------------------
A huge number of formulated products, domestic and commercial, are sprayed, and very few of them behave like water in the complex flow of a spray, even when they are mostly water.
We are talking here about viscosity - the resistance of a fluid to being deformed. A simple fluid like water, it doesn't matter how hard, how fast, or in what direction it is deformed, the resistance the water makes to that deformation is the same: the viscosity is a constant. We call these Newtonian fluids, because Issac Newton was the first white western man to publish in mathematical formulism, that the relationship between stress (the amount of force used to make the deformation) and strain (the amount the material deforms for that stress) is a constant.
In everyday life, we interact with many fluids that don't behave like that, at all. We expect toothpaste to flow out onto our toothbrush when we squeeze the tube, but then remain in a solid-like lump while we wet it under the tap, and then move the brush to our mouth. We'd be pretty upset if the paste just poured off the brush like water. Equally, we expect the paste to start flowing and not remain in a lump, once we start brushing. There are many similar foods examples, where you expect them to stay heaped on a spoon as though they were a solid, but then flow in your mouth (although the examples here are less international - custard and yoghurt work as familiar examples when I am doing training in the UK; I've variously used whipped cream, fondue and cheesecake in other locations).
Lots of formulated products work like this: the more force, or the faster you impose than force, the less resistance the fluid makes. The technical term for that is shear-thinning. It's an example of non-Newtonian fluid behaviour. Shear thinning arises because one more of the ingredients in the formulation is very finely dispersed into a liquid matrix - typically an oily or fatty ingredient dispersed in a water-based fluid. At rest, each of the tiny droplets of dispersed oil exerts a little bit of force on its neighbours. Imagine a crowd of people holding hands. When we deform it fast enough, the particles move away from each other so those weak bonds are broken (the people are pushed apart further than their arm's length, so they loose their grip), and now the fluid flows. When we stop moving it, the bonds may reform, and the solid-like beviour comes back - although not instantly - and in many materials the network never completely reforms to the name extent. This time-behaviour, rheologists term "thixotropy". Formulated products are often both shear-thinning and thixotropic.
Sometimes, the dispersed phase may impart the desired flow behaviour for the intended use of the product on it's own: but typically the formulator has to adjust the rheology, and often this is by adding rheology modifiers (thickeners) to the continuous phase.
Conventional laboratory rheometers can capture the complex flow behaviour in shear flow, but a feature of sprays is strong stretching (extensional) flows, both in the initial sheet formation, and especially, in the final stages of fluid ligaments collapsing into droplets.
Water and other simple fluids like honey, we can predict the resistance to stretching from a measurement of the resistance to shearing.
Complex fluids, we can't necessarily:- particularly when there are free polymer molecules in solution, and especially when those molecules are linear, with a flexible backbone, and moderate to high molecular weight. Polyethylene Oxide (or glycol) PEO/PEG is a classic example, an ingredient in many cosmetics and a common pharmacuetical excipient. Polyacrylamide is another example, found in several commercial applications. Chemically modified celluloses are another, often used as thickeners in aqueous coatings. Modified starches used in foods can be, although it depends on how branched they are. Again, some common examples, not an exhaustive list.
Solution polymers act like molecular "rubber bands". If you have a rubber band in your desk drawer, you can do this experiment now. Roll the band around between the palms of your hand. It rolls up into a ball. That's a model of shear flow, and a normal laboratory torsional rheometer. Now stretch the band between you hands. That's a model of extensional flow - and what is happening when a ligament of fluid is separating into drops, in the necks of fluid between adjacent incipient drops. The effect is most extreme at very low concentrations, when the molecules are separate from each other. As they become concentrated, they tangle (like balls of wool, or string), and the effect is reduced. Eventually when thhey become really concentrated, in a polymer melt, higher extensional rheology that expected from shear rheology re-emerges, but the casue if now the entanglement.
This of course means it gives very puzzling trends for dose-response formulation testing and design. At very low concentrations, there are too few polymer molecules in solution to have a significant effect, and no stretchyness is observed. Successive increases in concentration show increased stretchyness up to some maximum, and then quite an abrupt drop-off afterwards.
An aspect that makes this even harder to quantify, is that in a shear flow in a conventional rheometer, we will measure shear thinning, but in a spray, the fluid will respond by strain-hardening:- showing increased resistance to flow as the fluid is stretched harder. The shear rheology is still super-important to sprayability - the fluid needs to have the appropriate rheology to be pumped to and through the atomiser nozzle and form a liquid sheet, ligaments and drops. Appropriate shear rheology is a necessary but not sufficient condition for spraying. In an experimental design for a formulation trying to compare (some experimental measure of) spray performance with (some parameter from) experimental shear rheometry, the results will typically be at least inconsistemt, often apparently counter to expectation, frequently apparently completely random.
We care about this, as excessive extensional viscosity can give us various undesired effects: at worst a jet rather than a spray; perhaps just splatter, higher overspray, larger droplets, reduced coverage from larger droplets and narrower spray angle, poor patternation from banding (also called ribbing) in the spray, etc. It can also, if we are careful and subtle, give us a highly desired effect, of reducing width droplet size distribution - and hence reducing overspray.
However, it is hard to measure extensional rheology. In the late 1990s when I first encountered the issue (assisting some formulators trying to suppress misting in machining fluids), we had to use proxy methods, in that case observing the suppression of spray-fan angle. That worked (sort of) only because we wanted extravagant strain hardening in that application. Most of the challenges I see in spray formulation are the much more subtle tweaks needed to adjust droplet size distribution. By the time you have sufficient concentration of a sufficiently high molucular weight polymer to reduce the spray fan angle, you have already way, way overdosed it. Indeed, the trick is to make the addition subtle enough that you only see it in reduced overspray, not in changed spray patternation, coverage, etc.
Since then the field has rapidly progressed, largely driven by the development of a commercial instrument, the CaBER (Capillary Break-up Extensional Rheometer). There's a whole body of literature on this: if you want a starting point, I highly recommend Gareth McKinley's excellent review article Visco-Elasto-Capillary Thinning and Break-Up of Complex Fluids in Rheology Reviews from the equally recommended British Society of Rheology. You need to be a member (£25/year) to access the article at that link. That was published in 2005: plenty has developed in the last 20 years, but you will be able to follow those developments more readily with an understanding of the concepts and background in that article.
The CaBER is no longer manufactured, and anyway doesn't really have the range to measure rheology in the region applicable for sprays - we need to extrapolate from the measurments for insight. (If you already have a Haake CaBER, it is possible to extend the range significantly with mechanical, electrical and analysis software modification - get in contact for detials) Tri Tuledar still makes a faster version of the same technique, "Trimaster", originally developed to characterise ink-jet printer inks. Increasingly popular as it can be "home-made" with a syringe pump and a high speed camera is the "Dripping on Substrate Extensional Rheometer", see the work of Vivek Sharma at UIC for an introduction to this.
Limitations in all these techniques are (1) the strain rate is much lower than in a spray (or at least, in any spray I've ever seen in commercial applications) (2) you only measure one very small sample of fluid (often OK: may not be: it depends on the lengthscale and concentration of stuff in your formulation, and how homogeneous it is) (3) you need a REALLY fast (expensive) high speed camera to measure the subtle modifications you want for overspray reduction.
That's why we developed the Rayleigh-Ohnesorge Jet Extensional Rheometer.
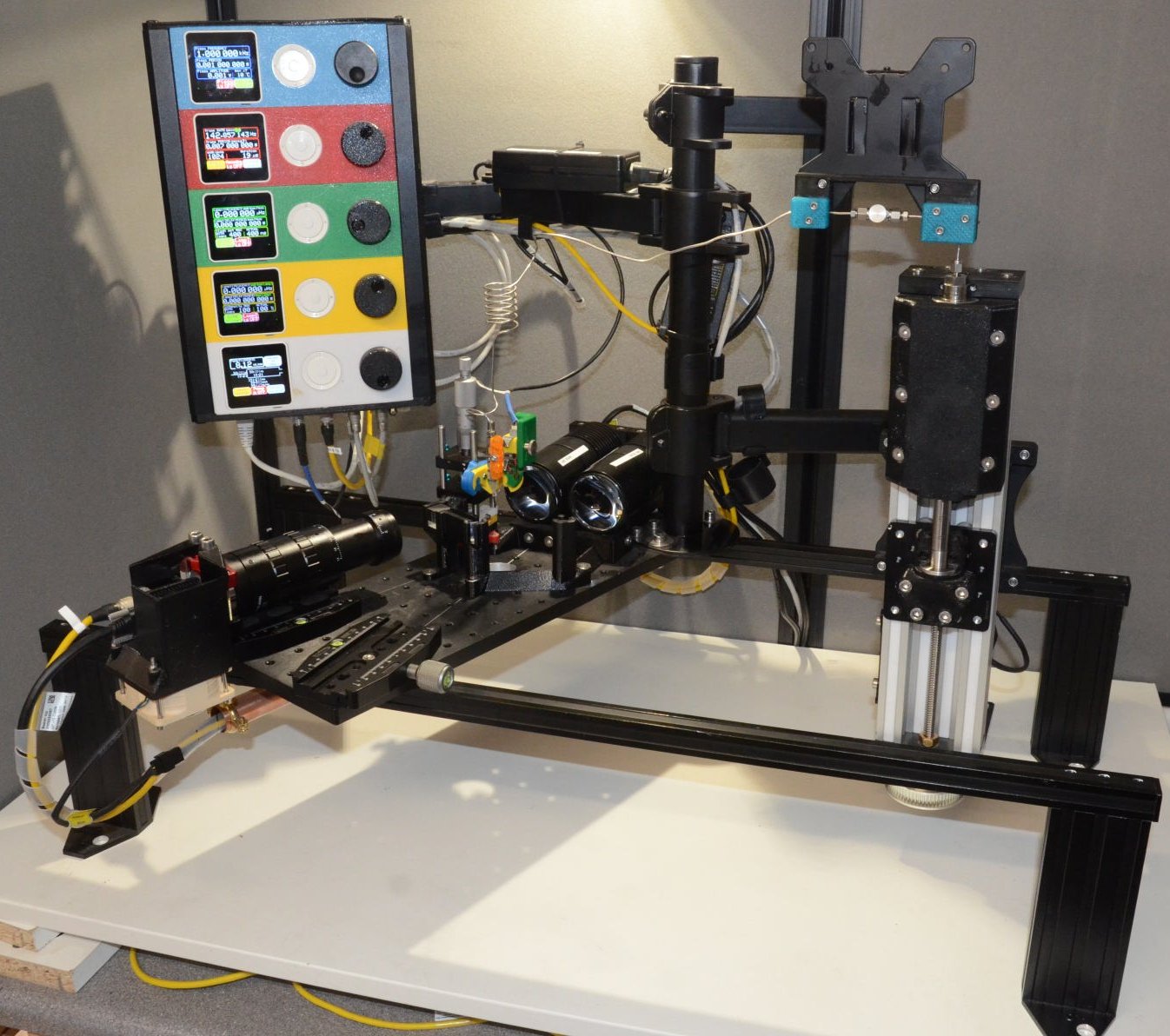
- Details
- Written by: Phil Threlfall-Holmes
- Category: Uncategorised
- Hits: 846
- TH Collaborative Innovation: TH Collaborative Innovation
The Rayleigh-Ohnesorge Jet Extensional Rheometer (ROJER) was developed in a project I led with Gareth McKinley at MIT, whilst I was still working for ICI and AkzoNobel.
We developed it to address the unanswered questions about the behaviour in extensional flows, of complex multi-component microstructured fluids - see page on extensional viscosity and spraying.
The ROJER considerably extends the range of strain rate and minimum relaxation time, when compared to CaBER and DoSER, which makes it exceedingly useful for characterising formulation rheology for spraying - especially, for engineering the very subtle formulation tweaking needed for spray droplet size control. However, the instrument was delicate and complex to use - making it only deployable in a handful of academic labs, and for measurements in-house at THCi in support of commercial client projects.
Motivated by that work for industrial clients, for a number of years we were developing a version for industrial laboratory use, as a back-burner project with Nik Kapur at The University of Leeds. see Greiciunas et al 2017 Design of a ROJER, JoR, 61, 3, 467 (and open access on whiterose.ac.uk).
We now have a version of the ROJER available for commercial purchase, which has been engineered for industrial laboratory use. A key feature is simultaneous orthogonal views of the jet. We dub this ROJER-X denoting both an eXtended method and the crossed views on the jet. Initially conceived primarily to address the numerous usability challenges that have limited the adoption of ROJER, especially in industrial research laboratories, we have additionally found exciting enhancement in capability, with the instrument specified to measure down to sub-microsecond extensional relaxation times. Whereas conventional capillary thinning techniques (CaBER, DoSER) observe a single fluid bridge, ROJER measures thousands of bridges a second, for many minutes of fluid flow from a syringe. This radically improves the statistics of diameter-decay curve fitting, and fluid sampling of real commercial formulations inhomogeneous on a single liquid bridge lengthscale. Such jets won’t remain stable in frame and focus for minutes: ROJER-X makes it practical to reposition and refocus on-the-fly: obtaining a time history of measured rheological parameters quantifying non-homogeneity. The two images of the same bridge can be synchronised, or be in fixed or phase delay from each other and/or the jet resonance driving frequency. This permits (a) cross-checking that it is truly a rheometric flow in 3D and remains in Rayleigh resonance, and of the image-analysis-derived rheological parameters; (b) a direct measure of jet speed, independent from a pump flowrate derivation; (c) a "coarse and fine" delay, simultaneous construction of the filament thinning curve, with more rapid acquisition and less fluid consumption.
Since all these operating modes are programmatically controlled through the custom controller, with streamed image acquisition, it also has the potential for real-time analysis (a unique capability for extensional rheometers), and eventually automatic setup and adjustment of parameters. These features are in active development.
- Details
- Written by: Phil Threlfall-Holmes
- Category: Uncategorised
- Hits: 753
- TH Collaborative Innovation: TH Collaborative Innovation
Spray training customised to your needs.
We have run 1 on 1 sessions, small group, and large group classroom sessions; both as on-site in person, and remote training; at multinationals, small businesses, and university groups.
The content is customised to what you need: typically including some aspects of spray science basics, terminology, physics; mechanics of atomisers relevant to your application; sprayed fluid physical properties, normally including some introduction to one of our specialties, coupling formulation, rheology and atomiser characteristics, formulating for sprayability, and/or low overspray. Often including some aspects of experimental rheometry, especially extensional rheology, and experimental spray characterisation; droplet sizing and imaging. For applications where the spray impacts on a surface, aspects of the statistics of droplet size, patternation, transfer efficiency and coverage; as well as rheology of spreading, levelling, slumping, film formation and drying/curing. For spray drying applications, considering droplet size and the interactions of drying kinetics, residence time and airflow patterns in a dryer; often including some discussion of the "Acoustic Atomiser" that I developed whilst at ICI (and now out of patent), for what is can teach us about spray dried product particle morphology control.
Expect the style of delivery to be influenced somewhat by your choice of the venue and size of the group. With a 1 on 1 or small group session at your site with access to your laboratories, we can adjust the content on-the-fly, and do hands-on demonstrations, and training on your characterisation instruments. A large group session, especially online, is likely to have a more pre-determined content, and more of a classroom style. Online, I can run some demonstrations from my lab; in a hotel or company conference room demonstrations typically have to be dry, or at most with water and consumer products.
Typically we are asked for technical training primarily for R&D staff, but normally with a spread of interests and backgrounds; so some of the participants may be senior managers or sales and marketing professionals, who want only to top-and-tail a high-level overview introduction and conclusion session; and we have structured training to be useful to hands-on laboratory technical staff, and well as experienced researchers seeking understanding of the complex physics and chemistry in spray science.
Phil teaches each year on the "Spray Drying and Atomisation of Formulations" CPD course at the The University of Leeds, where he is a Visiting Professor. This year it is 4-6 June 2024. Book your place now to avoid disappointment: the course is normally filled to capacity.
A popular aspect of that course is the lab demonstrations. It wasn't possible to do in-person lab demos for the 2021 course, so I made some video shorts.
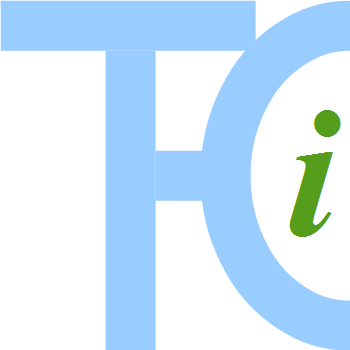
- Details
- Written by: Phil Threlfall-Holmes
- Category: Uncategorised
- Hits: 28146
- TH Collaborative Innovation: TH Collaborative Innovation
TH Collaborative Innovation (THCi) provides both a specialist technical consultancy in spray science-led innovation and also a facilitation service between industry and academic partners in research consortia projects across a range of process industry relevant applications. Combining years of experience working in multinational companies with continuing world-leading research, THCi helps businesses both large and small to optimise spray and dispense operations, for example by minimising unwanted spray mist and splatter by mechanical modifications to spray nozzles and tuning formulation rheology, thereby minimising waste and making sure more of the applied liquid ends up in the right place for the intended performance for you and your customers.